乾牛宝 缩小设备造出最大盾构机,打破国外垄断实现“绝地逆袭”
发布日期:2024-07-30 23:55 点击次数:148
摘要:“上海工匠”范连,发明了一套全新的设备和方法,解决了超大直径盾构机壳体加工的难题。
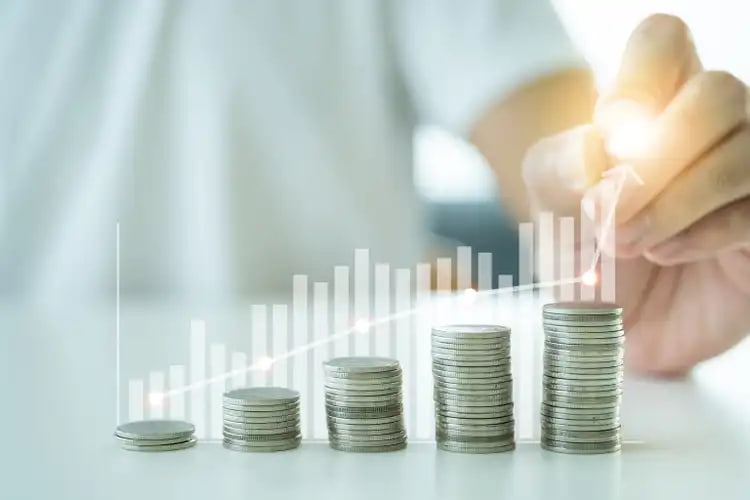
盾构机制造水平直接反映一个国家的地下隧道建设能力。近年来,国产盾构机频频打破纪录,其最大直径已超16米。然而,曾几何时,国产盾构的加工机床完全依赖进口,造价高昂不说,还处处受制于人。来自上海隧道工程有限公司的“上海工匠”范连,发明了一套全新的设备和方法,解决了超大直径盾构机壳体加工的难题。其成果首次应用于中国隧道直径之最的上海长江隧道,并成功实现“绝地逆袭”——不仅让曾经想高价出口我国设备的德国制造商刮目相看,还反向向我国请求购买代工服务。
打破国外垄断代
另辟蹊径以“小”制“大”
时间拨回2006年,上海在建上海长江隧道时,需要一台直径15.43米的盾构机,这个难题落在了范连所在的上海隧道工程有限公司。“15.43米的直径是当时世界最大,即使在今天也是第一梯队。”范连解释道,在当时,国内的地铁直径是6米3的直径,一般越江隧道直径在12米左右,一下从12米跨越到15米,对于技术和设备都是巨大的挑战。
按照传统经验,要制造一台盾构机,其生产机床就要比设备更大。然而,15.43米的直径已然创造记录,超1000吨的重量更带来不确定性,这样的机床放眼全国都找不到,如何解决?那时候,范连团队向着合作的德国制造商请教,但对方却“狮子大开口”,占着垄断优势,不仅要价超3000万,更无法保证工期。“我们也调研过市场,购买机床不会超过2000万元,但受制于技术能力,国内很难找到可以生产的厂家,即使有,也无法赶上工期,让我们陷入了被动。”
又要大、又要能承重,一时间,团队钻进了“牛角尖”。那段时间,范连每天都在琢磨这件事,和老师傅聊得最多的也是这个话题。有一天,他突然想到,“为什么一定要大呢?”虽然盾构机是大工件,但其内部是一个空心空间,“我就想有没有可能把机床放在盾构机的‘肚子’里,这样设备可以在盾构机壳体里‘打转’加工,既解决了尺寸问题,也解决了承重难题。”
这个从“大”到“小”的想法,一下子为团队打开了思路。团队研发了专用设备,还研发了独创加工工艺和专用软件。以此技术制造出的盾构机也成功应用于上海长江隧道。其后持续应用在南京、武汉、深圳等地多条大直径隧道建设工程,涉及盾构机总产值超过26亿元。
该设备的研发,成功实现了“绝地逆袭”,不仅打破国外垄断,相比国外工艺,精度提高40%,加工周期缩短一半。原本高高在上的德国制造商反过来向我国购买代工服务,从此,中国盾构产业也开始在世界立足。截至目前,成果已经向中铁装备、德国海瑞克等国内外制造商提供代工,带动产业发展。
历经三代技术更迭
实现从无到有到从精到强的飞跃
“这个项目的成功,实现的是从无到有的突破。”范连坦言,该项目虽然应用成功,但依然存在效率不高等问题。近年来,范连和团队先后将此技术进行了三次迭代,实现了从无到有、从有到精、从精到强的过程。
“第一代的原型机是将原有机床的各种部件拼装在一起做的改装,第二代则是进行了结构的重新设计,第三代是在第二代的基础上进行了数字化升级,实现从完全人工到半自动化到全自动化的过程。”范连介绍,在升级改造的过程中,团队也在不断尝试应用新技术、新方法。“比如在盾构机内部加工时,我们发现如果不先把设备先行固定,设备会因为‘马步不稳’发生位移,于是我们通过焊接将设备固定。起初,在确定设备位置时用的还是气泡式水平尺,效率和准确度都有限,从第二代起我们应用了激光跟踪测量技术,改进了工作流程。”
三次更迭,使设备的工作效率有了极大地提高,这套设备和方法乾牛宝,打破国外垄断并形成三大创新技术成果,授权实用新型专利1项。经中科院上海科技查新咨询中心评价具有新颖性,综合技术达到了国际先进水平。